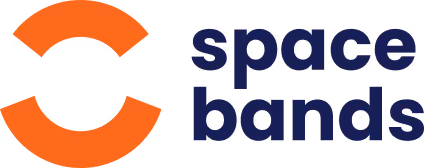
spacebands is a multi-sensor wearable that monitors external, environmental hazards, anticipates potential accidents, and gives real-time data on stress in hazardous environments.
Sign up to the mailing list:
Subscribe
Tracking the right health and safety KPIs (Key Performance Indicators) is the best way to stay on top of health & safety performance. KPIs provide insight into the organisations health and safety performance, and allow for effective performance measurement and improvement.
By tracking health & safety KPIs such as safety compliance, accident frequency, and safety training scores, employers can ensure that they are monitoring health and safety requirements and holding to standards. KPIs help health and safety teams prioritise health and safety activities, enabling them to identify areas of concern and focus on areas that need attention.
The National Institute for Occupational Safety and Health (NIOSH) offers research and resources to promote safe and healthy working environments.
With trackable health & safety KPIs, employers can leverage data to make smarter decisions and ensure that their organisation is as safe as possible.
Health and safety metrics measure performance against compliance KPI objectives, giving clear definition and examples of what health and safety success looks like. Indicators for measuring performance include important safety KPIs the number of workplace accidents, the number of days lost due to ill health, fire safety compliance, enforcement of safety protocols, and the number of safety audits conducted.
KPIs may vary depending on what technology is used and what industry the technology is used within, spacebands versatile health & safety device is suitable for a wide variety of hazards in industries such as construction, manufacturing, logistics and more.
Tracking health & safety KPI helps to prevent costly incidents, and can have a positive impact on a business’s bottom line. Companies need to ensure they have a robust set of health and safety KPIs in place for monitoring safety policies, identifying issues or trends quickly and ensuring their employees are kept safe.
A safety performance review should take place regularly to ensure policies are being followed and health and safety systems adopted where appropriate to monitor adherence to performance measures. There are plenty of resources available on the OSHA website (Occupational Safety & Health Administration).
Fatalities is one of the most commonly used safety KPIs to track safety standards. Fatalities reflect the direct impact of health and safety and serves to remind organisations of the potential cost of negligence.
The data obtained from the metric should be broken down to identify the major risks and their cause, as this will enable organisations to develop effective strategies to reduce the chances of fatalities occurring.
Tracking Fatalities is essential as it enables organisations to track their progress to achieving a safe working environment and to respond to any issues quickly.
The Total Recordable Incident Rate, often abbreviated to TRIR, is one of the most popular and widely-used KPIs when it comes to measuring and evaluating safety performance.
TRIR is not only an important indicator for health and safety performance but is also a key focus area for businesses and consortiums all around the world in 2023.
TRIR is a statistic which divides the total recordable incidents by the total number of hours worked - from which the total number of accidents per one million hours worked can be determined.
This metric allows for the accurate and continuous monitoring of workplace safety, as well as providing insight into areas for immediate improvement for any organisation.
In any health and safety management system, one of the most fundamental measurements of how well the system is working is the Lost Time Injury Frequency Rate (LTIFR).
This rate measures the frequency of workplace accidents that result in employees taking time off to receive medical treatment, or to be absent from work for any length of time due to a work-related incident.
This rate allows employers to compare the number of workplace injuries against the total number of hours worked, helping them to measure the effectiveness of their safety systems as well as identify areas of risk that require further attention.
In addition, the measurement of LTIFR helps employers to meet their health and safety targets and stay compliant with relevant regulations. By monitoring and acting on LTIFR figures, companies can make sure their workplaces remain accident-free, and their staff remain safe.
Lost Time Injury Incidence Rate (LTIIR) is one of the key safety performance indicators regularly tracked by many organisations. It is the number of lost-time injuries per million hours worked.
By tracking LTIIRs, organisations can understand the injury severity patterns, identify safety trends, and measure the success of their safety management systems.
Near Misses Rate shows how often an accident could have occurred in the workplace, but did not. This KPI is used to measure how proactive a safety management system is, as the goal should be to have no near misses at all.
By tracking the number of near misses, organizations can identify any areas of the workplace where safety needs to be improved, and implement the necessary changes.
Safety violation numbers can provide valuable insights into workplace safety. Within any industry, monitoring the number of safety violations is an important part of any safety management system.
By tracking this KPI, it is possible to identify weak points in processes or policies that can be addressed to improve safety. By monitoring this over time, companies can also identify patterns of worker behaviour that can be addressed through better training, or safety protocols that could be revised.
Equipment breakdowns in the workplace can be incredibly costly and are one of the leading causes of workplace accidents and fatalities. Measuring health of machines can improve the health of workers.
The Health and Safety Executive advises that employers monitor the rate of breakdowns across their organisation and take appropriate action to reduce incidents and enjoy the benefits of increased safety and decreased downtime and repair costs.
Equipment failure monitoring can be done through robust health and safety KPIs, with up-to-date records of all equipment, regular maintenance and testing procedures as well as an easy-to-implement system of incident reporting.
As the number of incidents related to vehicle fleets increase, it is essential that fleet safety measures are implemented to ensure the safety of employees and the public.
One of the key performance indicators (KPIs) used to track the performance of fleet safety is the number of collisions per million kilometres driven. This KPI can help measure if drivers are following safety regulations and highlight any areas of concern.
Penalties paid for breaches of health and safety regulations and policies is a key metric to track. As a consequence of irresponsible practices and lack of measures to ensure employee safety, employers can face hefty legal and financial penalties.
In addition to potential fines, insurance providers may also issue additional charges should the workplace be found to be in a higher risk category. As such, monitoring the number and amounts of penalties paid, as well as the costs, should form an integral part of any health and safety evaluation strategy.
No matter what size of business you have, managing attendance efficiently is an essential part of making sure your employees are engaged and productive. To help with this, we must have health and safety performance indicator(s) to track employee attendance rate.
Having key metrics in place will help identify any areas of concern and address them quickly and effectively. By using effective health metrics for monitoring health & safety, organisations can use employee attendance rate KPIs to minimise absenteeism, reduce any production inefficiencies, and increase employee satisfaction.
In addition, they can also use attendance KPIs to ensure reasonable working hours, avoid fatigue, improve overall productivity and ensure health and safety standards are met.
An organisation's success in promoting a culture of health and safety hinges on the visible commitment demonstrated by leadership. Through surveys, employee feedback, and open communication channels, companies can assess whether employees believe that management values their well-being and actively participates in health and safety success.
By monitoring this KPI, businesses gain insights into the effectiveness of their efforts to build trust, engage employees, and align everyone toward shared health and safety goals.
While occasional overtime may be essential, sustained periods of high overtime can result in burnout, heightened stress levels, and an erosion of the balance between work and personal life.
Evaluating the average number of overtime hours per individual offers meaningful perspectives into whether employees are enduring a continual excess of work and if professional commitments are intruding upon their personal time.
By striving for equilibrium between work responsibilities and personal well-being, businesses can foster the mental and physical health of their employees, leading to increased job contentment, productivity, and an overall positive company atmosphere.
Safety prevention costs are the financial investments an organisation makes on a monthly basis to proactively prevent health and safety incidents. These prevention costs encompass various aspects, including training programs, safety equipment procurement, risk assessments, and maintenance of safety infrastructure.
By tracking and analysing these ongoing expenses, companies gain insights into the resources dedicated to averting potential workplace hazards and fostering a culture of safety.
Monitoring monthly prevention costs allows organisations to assess the alignment of their financial commitments with the overarching goal of safeguarding employee well-being and operational continuity.
This metric provides a valuable gauge of how well your health and safety initiatives are functioning in tandem with overall productivity.
The 'Productive Days Percentage' reveals the proportion of days when employees are able to perform their tasks without disruption due to health and safety incidents. A higher percentage implies smoother operations and a reduced likelihood of work disruptions caused by accidents or injuries.
By monitoring this KPI, organisations can not only ensure a safe working environment but also enhance operational efficiency. A lower 'Productive Days Percentage' can serve as an early warning sign, prompting a closer examination of health and safety protocols to pinpoint areas for improvement and maintain a harmonious balance between employee well-being and business productivity.
This category encompasses the continuous education and preparation provided to employees regarding safety protocols, hazard awareness, and emergency response procedures.
Monitoring the progress of employee training is a direct reflection of an organisation's commitment to equipping its workforce with the knowledge and skills needed to navigate potential risks.
By tracking metrics such as training completion rates, frequency of refresher courses, and assessment scores, businesses can ascertain the level of employee preparedness. A robust 'Employee Training' sub-section not only fosters a safer work environment but also empowers employees to actively contribute to the organization's safety culture, reinforcing the collective goal of minimising workplace incidents.
This metric serves as a direct measure of an organisation's commitment to instilling a culture of safety from the top down. The percentage of trained management members reflects the extent to which leadership is equipped with the knowledge and tools to guide the implementation of robust safety protocols throughout the workforce.
A higher percentage indicates a proactive stance toward creating a secure environment, fostering employee well-being, and adhering to regulatory requirements. By ensuring that management is well-versed in health and safety practices, companies can champion a culture where safety becomes integral to decision-making processes, trickling down to every level of the organization and reinforcing a collective dedication to minimizing workplace risks.
Time to resolution or risks provides valuable insights into how promptly an organisation addresses identified risks and issues related to health and safety.
The average time to resolution reflects the agility of an organization's response mechanisms and its commitment to swiftly mitigating potential hazards.
A shorter average time implies a proactive approach to risk management, fostering a safer environment for employees and reducing the likelihood of accidents. By tracking and reducing this metric, businesses not only enhance employee well-being but also demonstrate their dedication to maintaining a work environment where potential threats are swiftly identified and effectively addressed, ensuring smoother operations and improved overall safety.
Health & safety is more than a tick box exercise followed to pass health and safety inspections. The importance of measurement in health and safety is paramount to success, if you can't track instances, then you won't be able to measure for any of performance indicators listed above, or any other KPIs.
spacebands track a range of safety and well-being features, and record instances of near misses to an analytics dashboard. This can enable employers to identify areas in need of operational improvement and track health & safety metrics over time.
Q1: Why are health and safety KPIs important?
Health and safety KPIs (Key Performance Indicators) are crucial for organisations in 2023 to ensure compliance with regulations and maintain a safe workplace. These KPIs provide insights into health and safety performance, allowing for effective measurement and improvement. By tracking metrics like safety compliance, accident frequency, and safety training scores, businesses can prioritise safety initiatives, identify concerns, and make data-driven decisions to enhance overall safety.
Q2: What are some examples of health and safety KPIs to track?
Organisations should track various health and safety KPIs, such as workplace accidents, days lost due to ill health, fire safety compliance, safety protocol enforcement, and safety audits conducted. These KPIs provide a comprehensive view of safety performance and help prevent incidents, ultimately impacting the bottom line positively.
Q3: Why is tracking Fatalities a significant safety KPI?
Fatalities, the key safety KPI, underscores the direct impact of health and safety negligence. Tracking the number of fatalities in the workplace over specific time periods helps organisations understand risks, identify causes, and develop strategies to prevent such occurrences.
Monitoring Fatalities reminds businesses of the importance of maintaining a safe working environment and enables swift responses to emerging issues.
Q4: What is Total Recordable Incident Rate (TRIR)?
Total Recordable Incident Rate (TRIR) is a widely-used KPI that measures safety performance by dividing total recordable incidents by total hours worked. This metric enables continuous monitoring of workplace safety, pinpointing areas for immediate improvement.
Q5: What is Lost Time Injury Frequency Rate (LTIFR)?
Lost Time Injury Frequency Rate (LTIFR) gauges the frequency of workplace accidents resulting in time off for medical treatment. This KPI measures safety system effectiveness and identifies areas of risk that need attention. By monitoring LTIFR, companies can meet safety targets, comply with regulations, and foster a safer work environment.
Q6: How does the Near Misses Rate KPI impact safety management?
The Near Misses Rate KPI measures proactive safety management by tracking potential workplace accidents that were narrowly avoided. Organisations should aim for no near misses, promoting a proactive safety culture.
Q7: Why is tracking Equipment Breakdowns important for workplace safety?
Equipment breakdowns are a leading cause of accidents and fatalities. Monitoring the rate of equipment breakdowns is vital to minimise incidents, downtime, and repair costs. By using health and safety KPIs to track equipment failure rates, businesses can ensure safer workplaces and more successful operations.
Q8: How does Fleet Safety (Collisions per million km driven) impact workplace safety?
Fleet safety is crucial for vehicle fleets in organizations. Tracking collisions per million kilometres driven helps measure compliance with safety regulations and highlights areas of concern.
Q9: Why is tracking Penalties Paid important for future workplace health and safety?
Tracking Penalties Paid for health and safety breaches is vital to avoid legal and financial consequences. Penalties can result from negligence, leading to hefty fines and insurance charges. Monitoring this KPI helps businesses remain compliant, financially sound, and focused on maintaining a safe workplace.
Q10: How does tracking Employee Attendance Rate promote workplace health?
Monitoring Employee Attendance Rate is essential for maintaining a healthy and engaged workforce. Efficient attendance management ensures productive operations, minimises absenteeism, and enhances employee satisfaction. By tracking this KPI, businesses can optimise working hours, prevent fatigue, and foster a safe, happy workplace.
Q11: What does Employee Perception of Management Commitment KPI measure?
The Employee Perception of Management Commitment KPI assesses how employees perceive their management's dedication to a safe work environment. This KPI reflects leadership's commitment to safety, trust-building, and fostering a secure workplace culture. Tracking this metric provides insights into employees' trust and engagement levels.
Q12: How does Average Overtime Hours Per Person impact workplace well-being?
The Average Overtime Hours Per Person KPI measures the balance between work and personal life. Tracking this KPI helps prevent burnout, stress, and diminished well-being due to excessive overtime. Striving for a healthy balance enhances job satisfaction, productivity, and overall company morale.
Q13: Why is tracking Monthly Health and Safety Prevention Costs important?
Tracking Monthly Health and Safety Prevention Costs reveals the financial investments in proactive safety measures. This KPI encompasses training, equipment, risk assessments, and maintenance expenses. Monitoring these costs aligns financial commitments with safety goals, ensuring employee well-being and business continuity.
Q14: How does the Productive Days Percentage KPI impact operational efficiency?
The Productive Days Percentage KPI measures the proportion of workdays without disruptions from health and safety incidents. Tracking this KPI ensures smoother operations, reduced disruptions, and enhanced efficiency. A higher percentage signifies a safer, more productive workplace.
Q15: What does the Employee Training KPI reflect?
The Employee Training KPI assesses the organisation's commitment to equipping employees with safety knowledge. Tracking training completion rates, refresher courses, and assessment scores ensures preparedness. This KPI empowers employees, fosters a safer work environment, and supports the organization's safety culture.
Q16: Why is tracking the Percentage of Management Trained in Health and Safety important?
The Percentage of Management Trained in Health and Safety KPI reflects the organisation's commitment to safety from leadership down. A higher percentage signifies a proactive approach to safety, regulatory compliance, and a culture where safety is integral to decision-making at all levels.
Q17: How does tracking Average Time To Resolution of Risks and Issues KPI impact safety?
The Average Time To Resolution of Risks and Issues KPI measures the promptness of addressing safety concerns. Reducing this time enhances agility in risk management, minimises accidents, and ensures a safer work environment. Tracking this KPI demonstrates dedication to swift hazard mitigation and improved overall safety.
We think you'll also find the articles below really useful
Join 5,000 H&S professionals and sign up for the spacebands monthly newsletter and get the latest blogs, free resources, tools, widgets and a dose of health & safety humour.
spacebands is a multi-sensor wearable that monitors external, environmental hazards, anticipates potential accidents, and gives real-time data on stress in hazardous environments.