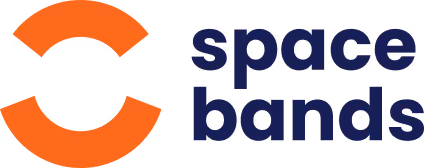
spacebands is a multi-sensor wearable that monitors external, environmental hazards, anticipates potential accidents, and gives real-time data on stress in hazardous environments.
Sign up to the mailing list:
Subscribe
We speak with Vincent Butler, owner of RSVP Safety Services Ltd and Safety & Health Activist + Innovator, to get his industry expert opinion...
I’ve been working 50 years | 20 years in deep coal mining starting age 16 in 1974 as a mining apprentice | 20 years heading up Health & Safety in SSE’s contracting division | 10 years freelance H&S consultant in a variety of sectors including building engineering services / construction / space & robotics
I became an elite/expert first aider in the coal mines age 16 and St John Ambulance to national competition standard and a qualified instructor still in my early 20’s.
My mining career progresses from coal face worker and volunteer trade union safety rep to mine shotfirer, then deputy, then shift overman. I moved mines in 1990 to become the mine safety officer at my new workplace.
I worked about 6 months as a colliery safety officer and was then surprisingly appointed as statutory mine undermanager. The primary legal focus of mine deputy and mine undermanager was the health, safety and welfare of working people and operations.
At the closure of deep coal mining, I was moved across to manage a skill training centre to re-skill mine workers being made redundant in trowel \ timber \ security \ welding \ pipefitting \ multi-skilled trades.
The organisation needed a safety person, so I volunteered, was sent off to do my NEBOSH National General Certificate 1993.The funding stopped for the training centre, redundancy was forced; part of my leaving package was further training, British Coal funded me with 6 months salary and all of the costs and literature to do the NEBOSH National Diploma in 1994 in one go.
British Coal found me the job opportunity as Health & Safety Manager for Southern Electric Contracting (SEC) where I worked for the next 20 years changing the world.
Reading / learning / asking / checking / curiosity / practical application / sharing with whoever will listen, then act.
My three big topic sets are:
1. the harm work does to the people who do it
2. silicosis
3. Mental health & well-being used as palliative & tertiary interventions instead of good, proper, meaningful, secure work that is safe, healthy & well paid.
All of my life for as far back as my memory goes, I’ve always been the one who makes people, in particular the bosses & leaders look at the dreadful stuff going on and asking the really awkward questions.
I have no idea why I’ve got that trait as I’d usually avoid confrontation; but if something ain’t right, I HAVE to say something about it!
I’m always busy on LinkedIn with posts and comments mostly about the three main items listed above.
I’ve produced a talk “beware the law of unintended consequence” regarding the resurrection of silicosis into the construction industry from the 1990’s onwards.
I’ve done my talk in Hong Kong and taken the principles to Singapore | Thailand | USA.
2009 to 2011 I was elected President of the Energy Sector of the Prospect Union; the old Engineers & Managers Association union from the UK’s Electricity Industry. I’ve been a Prospect NEC member for about 16 years through my work life.
Curiosity – having to know how everything works and its interrelationship with everything else; if you don’t know, how do you risk assess it?
That curiosity came up with:
• the podium access platform
• safety harnesses on overhead linesmen 10 years before the work at height regulations and first in the UK
• the two part electrical safety glove and protector to prevent arc flash injury
• the hop-up & step-up products
• Kevlar gloves on electricians
• full week residential H&S induction for new apprentices
• zero-time incident reporting
• the plan + control + RSVP language around risk assessment.
• IOSH Managing Safely & CITB SMSTS with 2 day enhancement for 1,200 supervisory, management & executive staff
• hazard-spotting-reporting
• tri-ennial H&S training for all field/site staff
Sales – getting people to buy into concepts, ideas, activity, results that they might not naturally want to do with enthusiasm, passion and detail. Not in a spivish way, being evidenced based, factual, straightforward with integrity and a stated ‘end-game’.
Doggedness / Tenacity / Bravery / Stoicism – keep going, if the idea or plan isn’t getting the desired outcome, try another way, use other people, sow-the-seed then get back to it later, make it look as if it was someone else’s great idea, be humble and “lose a battle to win a war”!
Competence – practically and actually, really know your stuff and mastery being a mix of knowledge + technique + skill + ability + application.
Know your limits – outside own competence & mastery – ask those more expert and masters in that topic see how their expertise is applied to my/our work.
20 years of hard, grinding, brutal work at the coal face with lots of deaths, accidents, injuries and harm to self and others gives a deep and meaningful appreciation, lived experience and empathy with working people – the balance, the sense, the practicality, the relevance, the specifics, the value and the proportionality of doing the H&S job properly so everyone really ‘gets-it’ what you’re trying to achieve is massively enhanced.
Without doing the ‘hard-yards’ for 20 years – its doubtful my impact in H&S would have been so immediate and significant.
Maybe not behind, but pretending safety is important was/is dangerous – having all the right words, the right documents, the right initiatives, the big-bosses doing their thing – BUT – behind the scenes, when no one is looking, carnage is going on, then when something dreadful happens, the “big-cover-up” starts – that will almost always end in disaster; think BP and the catastrophes they’ve been involved with over the past few decades.
I’ve worked in Petro-chem and process industries – the pretense and frankly bullshit almost always ends in catastrophe. Pointing it out is almost commercial suicide.
Asbestos management in the UK is shockingly bad. Putting 2,500 contracting electricians to work in 1,000 different workplaces every few days to break apart the client’s assets, premises and buildings – the body of accurate and up-to-date asbestos information is generally woeful and dangerous.
Break the work content down into its broad component parts – then risk assess, plan and control each component of the work.
The most significant changes were the purchase of fume cupboards and fit-2-fit respirator training for the use and application of very nasty chemicals | workshop machinery | lone working | class-4 lasers out in public areas on an airfield.
The provision and use of work equipment and machinery guarding requirements to keep people and robot arm movements separated and segregated by engineering interventions.
Tragic & funny: guy changing electricity meter located in kitchen cupboard. Laying on the floor, twisted into meter position back of cupboard, pushed cupboard door back and it trapped a pan handle on the cooker.
The pan of boiling stew fell into his lap, he jumped-up, off with is work trousers and underwear, but trousers got stuck at his safety boots, screaming blue murder, the lady of the house rushed-in took in the scene, realised the guy was in fact badly scalded/burned, got him into a cold shower to cool the burnt area.
The pain relief noises were heard by the man of the house arriving home from work, he enters the bathroom finding his wife showering our guy naked from the waist down.!!
Lots of burn treatment, skin grafts and scars and the injured person gave permission to use the story on our company newspaper at the time.
A mix of initiatives all coming together, primarily the growth of hazard spotting reporting with an intervention.
The IOSH Managing Safely qualification with then my two day extra “practical application enhancement” for all supervisors, managers and executives helped leverage the “no-where-to-run-and-no-where-to-hide-and-no-excuses-culture” – everyone responsible for planning, controlling and putting people to work knew: who, what, when, how, why, where and if of that function
The profits and business performance measures were the best in the sector by some significant margin according to Dun & Bradstreet analytics.
The initial idea was to reduce any down time or aborted visits to site by planning & controlling work much better so the electricians worked rather than not work because they had the wrong access kit or the wrong keys or the wrong components, or no parking had been arranged, or nowhere to put waste, those kinds of things.
Basically we got paid for doing stuff, no pay for not doing stuff – the improved safety performance was basically a by-product of better planning & control of operations and work.
Analytics to spot trends and poor risk judgement – some of the AI coming along will be a game-changer; I used to do that all long hand; 35,000 hazard spotting reports every year all categorised and logged into spread sheets and reports.
www.hazardscampaign.org.uk most trade union H&S resources are exceptionally good and well presented.
www.hse.gov.uk the hse’s coshh e-Tool is a great resource.
Dr Dom Cooper’s work
Curiosity + internet + exhibitions + social media
The best bit of kit on earth in H&S today is the Guarda Edge Power Cutter with their patented dust + fume + slurry control system – if widely adopted, it will save literally 10’s of thousands and lives from silicosis for a fraction of the cost of providing respiratory protective equipment.
Doing health and safety advisory and influencing work for a living isn’t ‘just a job’, it’s a life’s calling – I’m working for 50 years now and as enthusiastic and passionate as ever.
I still say my piece and still attend training, seminars, conferences, exhibitions and always ask the most questions, the ones others want to ask but are scared or maybe intimidated to ask!
Evidence-based facts and learn about “the laws of fiduciary duty – profit at any cost” – the best H&S ideas go away and die; I’d bet most times the ‘money people’ who allocate resources don’t get it!
Articulate the benefits and exactly what to expect for the investment | plan & control implementation | monitor the outcomes to prove absolutely its worked as planned, or not as the case may be, but we have the reasons why? | use relevant + specific + valuable + proportional (RSVP) in setting out the business case.
In 50 years of work; I’ve probably been involved in some kind of technical | vocational | refresher | new-skill | academic | ancillary education, training, learning for 35 of them.
Just before my 65th birthday, I attended the HSE labs in Buxton to do their practical CoSHH risk assessor’s course.
Lifelong learning is critically important and don’t ever be scared or embarrassed to ask – there’s no daft questions, but there’s lots of daft injuries!
A significant one as time moves along and AI gets better and better – the stuff Karl Symonds with FYLD is doing looks like it’s a game-changer for H&S at work, in particular around utilities sectors.
We think you'll also find the articles below really useful
Join 5,000 H&S professionals and sign up for the spacebands monthly newsletter and get the latest blogs, free resources, tools, widgets and a dose of health & safety humour.
spacebands is a multi-sensor wearable that monitors external, environmental hazards, anticipates potential accidents, and gives real-time data on stress in hazardous environments.