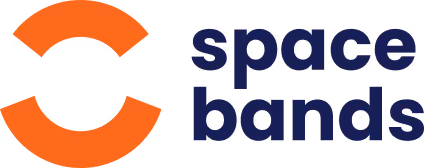
spacebands is a multi-sensor wearable that monitors external, environmental hazards, anticipates potential accidents, and gives real-time data on stress in hazardous environments.
Sign up to the mailing list:
Subscribe
Imagine a bustling factory floor, where machines hum and parts whiz by. While this environment fuels productivity, it also harbors a hidden danger: machine collisions. These incidents, when a machine collides with another machine, an object, or even a person, can have devastating consequences.
According to the Bureau of Labor Statistics, in 2021 alone, there were over 5,000 nonfatal workplace injuries involving machinery. While these numbers highlight the seriousness of the issue, even one collision is too many. Thankfully, through a combination of proactive measures and safety awareness, we can significantly reduce the risk of machine collisions and ensure a safer work environment for everyone.
Before diving into preventative measures, it's crucial to understand what constitutes a machine collision and the different types that can occur in a workplace setting.
Simply put, a machine collision happens when two or more machines, objects, or even people come into unintended contact, causing damage, injury, or even death. It's important to note that not all collisions are created equal:
By understanding these different types of collisions, we can better appreciate the diverse safety measures needed to create a truly comprehensive prevention plan.
The first line of defence lies in incorporating safety features directly into the design and selection of machinery. This proactive approach minimises the risk of collisions before they even occur. Here are some key examples:
These engineering controls form the foundation of a safe work environment, but they cannot operate in a vacuum.
Establishing clear workplace safety protocols is equally crucial. This involves:
By combining these engineering and administrative controls, we create a robust system for preventing machine collisions.
The success of any safety plan hinges not just on technical solutions and procedures, but also on the active participation of the workforce. Fostering a culture of safety requires:
By fostering a culture of safety and empowering employees to take an active role in preventing collisions, workplaces can create a safer environment for everyone.
Machine collisions pose a significant threat in workplaces, but they are not inevitable. By implementing a comprehensive strategy that combines engineering controls, administrative measures, and fostering employee engagement, we can significantly reduce the risk of these incidents and create a safer environment for all workers.
Remember, prioritising safety is not just a responsibility, it's an investment. The cost of preventing a single machine collision, both in terms of human suffering and potential financial repercussions, far outweighs the cost of implementing preventative measures. By taking proactive steps today, we can build a safer tomorrow for everyone in the workplace.
This blog serves as a starting point for further exploration. Numerous resources are available from organisations dedicated to workplace safety, offering detailed guidance and best practices. Here are a few examples:
Let's work together to make every workplace a collision-free zone, where everyone can focus on their tasks with peace of mind.
We think you'll also find the articles below really useful
Join 5,000 H&S professionals and sign up for the spacebands monthly newsletter and get the latest blogs, free resources, tools, widgets and a dose of health & safety humour.
spacebands is a multi-sensor wearable that monitors external, environmental hazards, anticipates potential accidents, and gives real-time data on stress in hazardous environments.