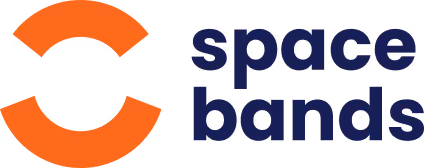
spacebands is a multi-sensor wearable that monitors external, environmental hazards, anticipates potential accidents, and gives real-time data on stress in hazardous environments.
Sign up to the mailing list:
Subscribe
In today’s workplaces, ensuring the health and safety of employees isn’t just a legal requirement—it’s an ethical obligation. For industries where machinery and tools produce vibration, exposure to such hazards can lead to serious health problems. To address this, the Control of Vibration at Work Regulations 2005 were introduced, aiming to minimize vibration-related risks. This blog dives deep into the regulations, their importance, and how businesses can ensure compliance.
Introduced as part of broader workplace health and safety laws, the Control of Vibration at Work Regulations 2005 were designed to protect workers from exposure to excessive vibration. The regulations primarily focus on two types of vibration:
The regulations are particularly relevant for industries such as construction, manufacturing, engineering, forestry, and mining, where vibration exposure is a daily risk.
To comply with the Control of Vibration at Work Regulations 2005, employers must fulfill several critical responsibilities:
Employers are required to assess the risks associated with vibration exposure. This includes identifying tasks and tools that could pose a risk and determining the level of exposure employees face.
Exposure levels are categorized by two thresholds:
If you'd like to learn more about how to calculate exposure levels, we've already written that blog for you.
Employers must implement control measures to minimize vibration exposure. This could involve upgrading to lower-vibration tools, introducing job rotation, or enforcing regular breaks.
Employees should be made aware of the risks of vibration exposure and trained on safe work practices. Clear communication about the hazards and preventive measures is essential.
Employers need to document risk assessments, exposure levels, and the measures taken to reduce risks. Regular reviews ensure the measures remain effective and up-to-date.
Exposure to vibration over time can lead to debilitating conditions:
You can learn more about the tiers of HAVS exposure and what you can do about it in this blog.
Non-compliance with the regulations can result in:
You can check out the highest hand arm vibration claims here.
Identify tools and tasks with the highest vibration levels. Measure exposure using tools such as vibration meters and calculate daily exposure levels.
Use monitoring tools and software to track vibration levels over time. Maintaining accurate records is crucial for demonstrating compliance and protecting your business during inspections or audits.
Provide training on:
Modern technology makes compliance with vibration regulations easier. Solutions like wearable devices monitor real-time vibration exposure, and analytics dashboards allow employers to track data and identify risks early. For example, products like spacebands can alert users when they are approaching EAV or ELV limits, ensuring safety and maintaining compliance.
Here are the top 10 ways to prevent HAVS in your workplace.
A construction company ignored vibration risks and failed to monitor exposure levels among its workers. Several employees developed HAVS, leading to a fine of over £100,000 and permanent damage to their health.
In contrast, an engineering firm introduced low-vibration tools, job rotation, and wearable monitoring devices. The result? Reduced health issues among employees and a clean safety record during HSE inspections.
As technology advances, the tools available for vibration control are becoming smarter and more effective. Key trends include:
The Control of Vibration at Work Regulations 2005 are essential for safeguarding workers' health and maintaining a safe working environment. By conducting thorough risk assessments, implementing effective control measures, and leveraging modern technology, employers can ensure compliance and protect their workforce.
It’s not just about avoiding fines—it’s about creating a workplace where employees can thrive, free from preventable health risks.
Take action today! Assess your workplace vibration risks, explore modern monitoring tools, and stay compliant with the law.
We think you'll also find the articles below really useful
Join 5,000 H&S professionals and sign up for the spacebands monthly newsletter and get the latest blogs, free resources, tools, widgets and a dose of health & safety humour.
spacebands is a multi-sensor wearable that monitors external, environmental hazards, anticipates potential accidents, and gives real-time data on stress in hazardous environments.