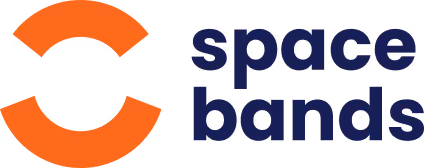
spacebands is a multi-sensor wearable that monitors external, environmental hazards, anticipates potential accidents, and gives real-time data on stress in hazardous environments.
Sign up to the mailing list:
Subscribe
We speak with Hugh Maxwell owner of Maxwell Safety Solutions and all round H&S influencer, to get his industry expert opinion...
Leaving Heriot-Watt university with a degree in Chemistry, my initial interests lay in continuing development in this area.
The company I joined, Foseco, manufactured specialty chemical products for the foundry and steel industry. I soon moved into Operations then Quality Assurance roles, before picking up Health, Safety and Environmental Management responsibilities in the early 1990’s.
This was a time of major focus change, and Foseco was owned by Burmah Castrol PLC at the time, who were keen to develop strong HSE standards. This enabled me to grow as a professional and take regional and later global responsibilities within the business.
In 2008 we were purchased by Cookson Chemicals, and I was appointed HSE Director for Vesuvius, a role I undertook until December 2017.
I left the business and took 8 months out supporting my wife in her battle against breast cancer. We were so lucky when she beat this major challenge. We agreed after this I would look for roles I both enjoyed, and which enabled me to give more back.
This leads me to where I am now – Maxwell Safety, leading a Cultural Change programme as an Associate of Fides Oak, working a month on and off rotation at the Anglo-American Platinum Mines in South Africa.
This still allows me to mentor, coach and support the development of others, including business elsewhere across Africa.
My current and future focus is to support the develop, growth and cultural maturity expansion of individuals, communities and organisations across Africa, India, Asia and the Middle East. This work is already underway in Kenya and next Nigeria as eastern and Western African hubs.
The business will grow and evolve to be the leading African risk and HSE consultant under our Safety Key Consultants Africa brand initially. Please see www.safetykeyafricaconsultants.com for more information.
Over my career I have been extremely fortunate to work in manufacturing, construction, steel, foundries, oil and gas, construction and mining.
My roles have focused on HSE and risk management, with invaluable insights and involvement in Business Development, Sustainability, Leadership and Strategic Management.
Now is very much a time for me to give back and share whenever I can. I am truly humbled for the recognition I have received from my work and achievements with others over the years. These include: IIRSM Mentor of the Year 2022 and 2019; IIRSM Best International Risk Initiative 2018; WSHAsia Top Safety Influencer 2023; SHP Health and Safety Influencer shortlist 2023 and 2021.
It is really surprising to me how my interests and development have brought me to where I am now.
Early days, despite entering the manufacturing world with strong qualifications, I maintained strong learning in areas such as Operations and Strategic Management, Total Quality Management (in which I hold a master’s degree), Environmental Management, Health and Safety and Sustainability and Business Management.
This all comes a full circle now and I have recently studied further in the areas of Mentoring, Coaching and Psychology, including Lumina Spark as a personal, team and organisational development tool.
It all comes back to people – they are ultimately the solution to most workplace and organisational issues. This is reflected in the large amount of time and effort I put into coaching, mentoring and developing myself and others.
Having worked as a HSE Consultant for several years now, I can truly say no two days are the same and the scope and depth of work and priorities depends on the needs of your customer and other stakeholders. This in itself keeps you fresh, tuned and hungry to give your best, be your best and bring the best out of others.
Prioritising and aligning your focus with the needs of your clients and their audiences is key – as too is ensuring you understand and meet their expectations as a minimum.
Constant planning, review and evaluation are key irrespective of what task or activities you are performing, training you are providing or whatever form of interaction you are undertaking.
Every day is a school day.
As a consultant in any field, I believe there is no one size fits all. Understanding the needs and expectations of your client are key, as too is establishing key deliverables and a structured approach and framework – depending on the work to be undertaken.
Strong technical competence, expertise and good analytical and problem-solving skills are all essential elements.
Making best use of the resources you have available and understanding what current resources are best for the task at hand.
Being flexible, resilient and adaptable when unforeseen issues arise.
Having an open learning mind, being able to listen intently and read situations and underlying factors.
Continually learning and developing oneself and others, gaining buy-in from clients, empathy, appreciating and understanding the business and industries you support, excellent communication, interaction and interpersonal skills, strong collaboration and teamworking capabilities and good strategic thinking and business awareness.
All of these elements form a part of the ongoing success as a health and safety consultant but equally important is knowing when you truly don’t know, not being afraid to share this and go away and gather the necessary information or alternatives to share.
Pulling all of these elements together as and when needed will ensure you gain the level of trust, maintain your integrity and integrity of intent and honesty as a professional.
There are some marked differences in different countries and continents, largely driven by the legislation and focus of enforcement bodies in the countries. However, we should note that even within the so-called developed world, the level of safety maturity, risk awareness and safety cultural maturity can vary significantly.
Never judge as even in the developing environments, there can be some really good takeaways to share in terms of working practices.
It is more a case of seeing legal compliance as a minimum standard on the safety journey and thereafter sharing as many best practices as possible, once buy-in and senior management portray the level of buy-in and safety leadership which is needed to drive the change.
Health and safety is a serious matter but this doesn’t mean that there is never time for a bit of light humour now and then. Over the years there have been a number of incidents which are worth sharing.
Early in my career in Health and Safety, I was responsible on a site where we had a number of minor eye injuries due to dust and fluids. By consensus, it was agreed that we should invoke 100% eye protection in all designated areas. This was well before this was the norm in many industries. We gained agreement with the Union.
However, on returning to work one night shift, the shift safety representative greeted me to see what I was doing there. I immediately noticed that the person was wearing his protective glasses, but he had removed the polycarbonate lenses and subconsciously was scratching his eye. You can imagine the range of expletives I shared with him emphasising that this was not acceptable and even worse behaviour coming from a safety representative.
There was also an experience I had in India in the early 2000’s which is worthy of mention. We manufactured a range of refractory paints for sand moulds in the foundry industry. Some of the paints were alcohol based.
The plant was located in a village called Sanaswadi, near Pune, right on the edge of a jungle. One day, one of the wild monkeys ventured into the plant and took a liking to the alcohol we were decanting. He got very drunk and quite aggressive throwing drums and other tools at our workers. I immediately called security and said can we take any action. One of the bosses suggested shooting him!
However, as many of the workforce were Hindu, this was frowned upon as Hanuman, in Hindu mythology, is the monkey God, the commander of the monkey army, revered as an avatar of Shiva. The decision was made we should wait it out and try to entice the monkey out with fruit and food.
It took over a day until the monkey decided to vacate the workshop, thanks to the food offerings and a trail of fruit into the jungle. The inebriated and staggering monkey meandered his way into the jungle never to be seen again.
Following this, shutters and access controls to prevent a reoccurrence were fitted to the work area! There was one I would never have expected in international health and safety work!
The most useful tools to implement health and safety measures is listening, observing and asking open questions.
Understanding the situation and challenges allows you to apply the simple methodology of the 3W’s – What can go wrong? Why can it go wrong? What can be done to prevent this going wrong?
Empathy, understanding and engagement in order to explore alternative solutions and prioritising needs must be a key shared objective.
Good planning of projects and associated activities is critical to examine, evaluate and establish the best solutions to specific hazards or activities.
This enables you to select the most appropriate technology available to mitigate or eliminate workplace hazards and risks, which could result in accidents, injuries or unsafe conditions.
A clear understanding and early engagement in project management is critical in order for the most appropriate controls and technologies to be applied.
There are some really useful and powerful tools and support information available today with both national and international applications.
It is important that you select ones that fit the needs, the size and the complexity of the business needs. One of the most useful free “Go To” resources I like to visit regularly is www.hse.gov.uk. There is so much great information there - not only legislation but guidance notes and ACOPs (approved codes of practice).
Some of the other regular “Go To” resources I use include SHP Magazine published on behalf of IOSH and the Sentinel published by IIRSM.
This assists with a good range of current and impending legislation articles, sharing best practices and new technologies and a broad range of interesting development information.
However, there are a number of other apps out there I believe truly invaluable, these include EcoOnline – supporting chemical management and COSHH needs; Barbour Consolidated (formerly CEDREC) for legislative and other products are good for legal updates and changes.
Again, Sentinel, SHP, WSHAsia are just some of a range of great publications I regularly refer to for new and innovative products.
Living in Lichfield I also try to attend a number of exhibitions including the Health and Safety Event at the NEC, or the Health and Safety Expo in London.
I also have a great relationship with the Safety Health Environment (SHE) Show, ran in 3 UK locations each year. Jeanette Marshall, Max and Vicky Washington run a great event at all locations, with great speakers and some great exhibitors. Well worth attending and valuable for networking.
I don’t attend every year but when I do I like to examine what is new on the market in terms of products. It is also a valuable opportunity to meet up with longstanding contacts and to meet new contacts for networking.
My personal needs are prioritised on a reliable phone, laptop and WhatsApp – especially when working remotely in South Africa and wanting to keep in regular contact with loved ones and friends.
This allows me to maintain a good level of engagement despite whatever time differences exist – power outages allowing!
It is so important to gain buy-in. Work on your powers of persuasion and base it on assessment of need and value add/benefits to the business. If you are able to involve or share success stories where tangible benefits have been achieved, then this is good to make a strong business case.
I have learned that we don’t always get what we want so to develop a strong business case and don’t be scared to include alternatives to the desired solution.
Sometimes you need to lose a battle to win a war and we all know resources are finite so make sure you build winning justifications for the business “must haves”.
Gaining trust and belief from stakeholders that the change will add benefit is so important, so honestly, open communication and getting them to buy into and feel to be one of the “change drivers” can also assist.
This may mean taking them to other businesses already benefiting from your intended investment. I have found this to be very useful on a number of occasions.
Change is one of the few constants we see in modern business, and nobody likes change imposed on them, so it is really important that we sell the benefits as early as possible to gain buy-in.
A strong case supporting the need for change should be made where people are allowed to share any concerns or fears.
Share the benefits to be gained and make the key stakeholders most effected by the change part of the implementation team. This promotes buy-in and ownership. Plan well, discuss openly, have as much transparency as possible, review progress regularly and address any small issues before they escalate.
A couple of things to avoid is implementing too many changes at the same time involving the same stakeholders as this will result in failure due to overload and increase work pressure needlessly.
Also, avoid implementing new technology just for the sake of it. You should undertake a baseline assessment first of where we are, are we ready for this change, what training and other resources may be needed and most of all are we as a business or part of the business ready for this change.
If not, there will be a lack of acceptance, or failed implementation.
It really depends on the nature of the business, as there are a range of different hazards to which people and businesses can be exposed.
Interesting one I face currently is in Platinum mining – high risk; confined spaces 1.5km underground, toxic and flammable gases, noise, dust, vibration, slips, trips, falls; moving equipment and heavy machinery, emergency preparedness for fall of ground and much more.
The only way to manage them is strong communication, pre-work planning and risk assessment, dynamic risk assessment underground and regular inspection and monitoring of workplace conditions and the environment.
I am a strong advocate of AI and the way it can be deployed and used across a range of industries to prevent accidents and save lives. Already, I have used and experienced some great applications of AI in steelmaking, construction, oil and gas and manufacturing in terms of many safety-related applications.
The application of AI-enabled safety technologies including drones, robotics, wearables, sensors, smart equipment is expanding rapidly. Much more expansion is being seen with augmented reality (AR) and virtual reality (VR) applications, computer vision, mobile applications and analytical software.
In many situations already we see hardware components collecting data (for example, sensors or detectors) or executing actions (robots). This is combined with software components relying on machine learning to analyse patterns and generate insights and predictive information concerning safety hazards.
The future will offer even more great opportunities to apply AI and we must utilise this fully to prevent accidents, incidents and save lives.
Business leaders should involve their Management and workforce in assessing such solutions and applications to improve industrial safety. It is so important that we create and build a culture and risk management profile within the business that is conducive to adopting the application of AI tech for safety purposes.
We hope you enjoyed this article, you can read and learn from other industry experts from across the globe, and learn from their insights into health & safety in a variety of industries.
We think you'll also find the articles below really useful
Join 5,000 H&S professionals and sign up for the spacebands monthly newsletter and get the latest blogs, free resources, tools, widgets and a dose of health & safety humour.
spacebands is a multi-sensor wearable that monitors external, environmental hazards, anticipates potential accidents, and gives real-time data on stress in hazardous environments.