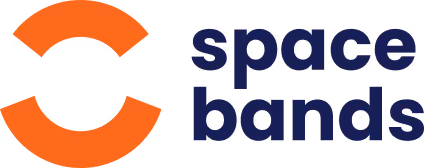
spacebands is a multi-sensor wearable that monitors external, environmental hazards, anticipates potential accidents, and gives real-time data on stress in hazardous environments.
Sign up to the mailing list:
Subscribe
Download your toolbox talk by clicking the button above and print it off to deliver to your team.
Hand-Arm Vibration Syndrome (HAVS) is a serious but preventable occupational disease that affects thousands of workers exposed to prolonged vibration from power tools and machinery. From construction sites to manufacturing floors, employees risk irreversible damage to their hands and fingers if proper precautions aren’t taken.
The good news? With the right training, monitoring, and control measures, HAVS can be prevented. As a Health & Safety Manager, it’s your responsibility to educate workers on the risks, symptoms, and best practices to reduce exposure.
This article provides a ready-to-use toolbox talk on HAVS training and monitoring—helping you deliver an engaging, effective safety session. Download the free HAVS Toolbox Talk PDF at the end of this post and equip your team with the knowledge to stay safe. Let’s dive in.
Hand-Arm Vibration Syndrome (HAVS) is a progressive and irreversible condition caused by prolonged exposure to vibrating tools and machinery. Over time, excessive vibration damages nerves, blood vessels, and muscles in the hands and arms, leading to numbness, tingling, loss of grip strength, and even permanent disability.
Workers are at risk of developing HAVS if they regularly use:
✅ Power tools (grinders, drills, jackhammers)
✅ Heavy machinery (compactors, chainsaws, sanders)
✅ Hand-guided vibrating equipment (concrete breakers, needle guns, impact wrenches)
The longer someone is exposed to vibration without proper protection, the higher their risk of developing HAVS.
HAVS doesn’t happen overnight—it progresses in stages:
Once HAVS reaches an advanced stage, there is no cure—which is why early detection and prevention are critical.
In the next section, we’ll explore why HAVS is a major workplace risk and the legal responsibilities employers must follow.
Hand-Arm Vibration Syndrome (HAVS) isn’t just a minor inconvenience—it’s a permanent, preventable disability that affects workers’ ability to do their jobs and live comfortably. Left unchecked, HAVS can lead to chronic pain, loss of hand function, and even job loss.
HAVS is a widespread issue in industries where workers use vibrating tools daily, including:
🏗 Construction – Drills, jackhammers, compactors
🔧 Manufacturing – Grinders, sanders, impact wrenches
🌳 Forestry & Landscaping – Chainsaws, trimmers, hedge cutters
🚘 Automotive & Engineering – Riveters, polishers, pneumatic tools
🛠 Utilities & Rail Work – Concrete breakers, rail maintenance tools
Workers in these industries may not notice the effects immediately, but over time, daily exposure builds up—leading to life-altering consequences.
Governments worldwide recognize HAVS as a serious occupational health risk and have introduced strict regulations to protect workers:
📜 UK: The Control of Vibration at Work Regulations 2005 requires employers to assess and limit vibration exposure.
📜 EU: The Physical Agents (Vibration) Directive (2002/44/EC) sets exposure action and limit values.
📜 USA: OSHA and NIOSH provide guidelines for reducing vibration-related injuries.
Failure to comply with these regulations can result in hefty fines, legal action, and compensation claims—not to mention the human cost of workers suffering permanent damage.
🚨 A UK construction company was fined £500,000 after multiple workers developed HAVS due to uncontrolled vibration exposure.
🚨 A manufacturing worker lost his job after developing severe HAVS, making it impossible for him to grip tools.
🚨 Thousands of workers experience life-altering disability each year simply because vibration risks weren’t properly managed.
In the next section, we’ll cover how to spot the early signs of HAVS before it’s too late.
Catching Hand-Arm Vibration Syndrome (HAVS) early is crucial to preventing permanent damage. The problem? Many workers ignore the first warning signs—only realizing the severity when it’s too late. By educating workers on symptoms and encouraging early reporting, employers can step in before lasting harm occurs.
Workers exposed to frequent vibration should watch for:
🟡 Tingling or Numbness – Fingers or hands feel "pins and needles," especially after tool use.
🟡 Loss of Feeling – Difficulty sensing textures or temperature changes.
🟡 Loss of Strength – Weaker grip, struggling to hold tools firmly.
🟡 White Fingers ("Vibration White Finger") – Poor blood circulation causes fingers to turn pale in cold weather.
🟡 Delayed Recovery – Symptoms persist for hours or even days after exposure.
At this stage, symptoms may come and go, but if vibration exposure continues, they become permanent—leading to serious consequences.
HAVS symptoms worsen in stages if exposure is not controlled:
🔸 Stage 1: Occasional tingling/numbness, minor impact on daily tasks.
🔸 Stage 2: Frequent numbness, difficulty with fine motor tasks (buttoning a shirt, holding small objects).
🔸 Stage 3: Severe pain, white fingers in cold, permanent nerve damage, inability to grip tools.
Once a worker reaches Stage 3, there is no cure—only management of symptoms. This is why early detection is key.
If a worker experiences HAVS symptoms, take action immediately:
✅ Encourage reporting – Workers shouldn’t fear repercussions for reporting symptoms.
✅ Reduce exposure – Adjust work schedules, rotate tasks, and ensure regular breaks.
✅ Provide medical assessments – Occupational health professionals can evaluate severity.
✅ Monitor vibration levels – Use wearable tech (like Spacebands) to track exposure in real time.
By identifying HAVS early and implementing control measures, employers can protect workers from lifelong disability.
In the next section, we’ll dive into practical strategies to reduce the risk of HAVS.
Preventing Hand-Arm Vibration Syndrome (HAVS) is all about reducing exposure and implementing the right control measures. Employers have a legal and ethical responsibility to protect workers, and by following best practices, they can significantly lower the risk of long-term damage.
🔧 Use Low-Vibration Tools – Modern power tools often have built-in vibration dampening. Choose equipment designed to minimize exposure.
🛠 Maintain Tools Regularly – Blunt or poorly maintained tools vibrate more, increasing risk. Keep them sharp, balanced, and in good condition.
🤲 Use Anti-Vibration Handles & Gloves – Some tools have specialized grips to absorb vibration. However, gloves alone are NOT a solution—they should be used alongside other controls.
⏳ Job Rotation – Rotate workers to prevent prolonged exposure to vibration.
✋ Regular Breaks – Encourage workers to take short breaks to reduce cumulative exposure.
💪 Improve Grip & Technique – Holding tools too tightly increases vibration transmission. Teach workers to grip firmly but not excessively.
📊 Measure & Track Exposure – Use vibration meters or wearable tech (like Spacebands) to monitor real-time exposure levels.
📚 Provide HAVS Training – Workers should understand the risks and recognize early symptoms.
🩺 Conduct Regular Health Surveillance – Regular medical checks help catch symptoms before they become severe.
Employers must comply with legal vibration exposure limits:
🔹 Exposure Action Value (EAV): 2.5 m/s² A(8) – Employers must take action at this level.
🔹 Exposure Limit Value (ELV): 5.0 m/s² A(8) – This is the maximum legal daily exposure.
If exposure is near these limits, control measures MUST be in place to protect workers.
By following these steps, companies can prevent HAVS, protect their workforce, and avoid costly legal consequences.
In the next section, we’ll discuss how HAVS monitoring and compliance technology can further enhance workplace safety.
Even with best practices in place, continuous monitoring is essential to ensure workers aren’t exceeding safe vibration exposure levels. Modern technology, such as wearable devices and digital tracking tools, can help employers stay compliant and proactively protect their workforce.
📊 Wearable Tech for Vibration Tracking – Devices like spacebands can track real-time vibration exposure, alerting workers and managers if safe limits are exceeded.
📱 Mobile & Cloud-Based Reporting – Digital platforms allow for easy tracking of worker exposure history, helping to identify high-risk individuals before symptoms develop.
📢 Instant Alerts & Warnings – Automated alerts notify workers when they need to take breaks or switch tasks to prevent overexposure.
🏥 Regular Medical Assessments – Routine health checks help detect early symptoms and prevent HAVS from progressing.
🖐 Self-Assessment Tools – Workers can use mobile apps or workplace checklists to report numbness, tingling, or grip weakness early.
📅 Periodic Risk Reviews – Regularly reviewing exposure data ensures safety measures remain effective over time.
✅ Automated Record-Keeping – Digital logs provide clear proof of compliance with Control of Vibration at Work Regulations (2005) and other legal standards.
💼 Audit-Ready Reports – In case of an inspection, having accurate, time-stamped exposure data can protect businesses from legal action.
💰 Cost Savings – Investing in HAVS prevention reduces compensation claims, lost workdays, and productivity losses.
By integrating technology-driven monitoring with traditional safety practices, companies can create a proactive, data-driven approach to HAVS prevention—ensuring both worker safety and regulatory compliance.
To make your next safety meeting easier, we’ve created a free, downloadable HAVS Toolbox Talk PDF. This resource covers:
✅ HAVS risks and symptoms
✅ Best practices for prevention
✅ Workplace safety checklist
By educating workers and leveraging smart monitoring solutions, we can eliminate preventable cases of HAVS and create safer, healthier workplaces.
We think you'll also find the articles below really useful
Join 5,000 H&S professionals and sign up for the spacebands monthly newsletter and get the latest blogs, free resources, tools, widgets and a dose of health & safety humour.
spacebands is a multi-sensor wearable that monitors external, environmental hazards, anticipates potential accidents, and gives real-time data on stress in hazardous environments.