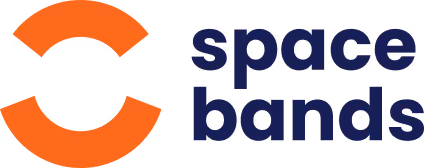
spacebands is a multi-sensor wearable that monitors external, environmental hazards, anticipates potential accidents, and gives real-time data on stress in hazardous environments.
Sign up to the mailing list:
Subscribe
We speak with Amandeep Beesla owner of Amandeep Beesla Consulting Ltd and all round H&S influencer, to get her industry expert opinion...
Amandeep was born and raised in Vancouver BC, Canada into an immigrant trucking family. She is a third generation, heavy equipment operator by trade with over 25 years of onsite field experience in heavy industrial construction, civil road building, pipeline, winter drilling, open-pit mining, earth works, live process plants, SAGD sites, infrastructure, transportation and trucking, petrochemical, and oil and gas field industry in Alberta, British Columbia, Saskatchewan, and Washington State and has been on international projects as part of global teams.
Amandeep is currently involved with the LNG Kitimat project in a health and safety capacity.
She is involved with various executive boards, committees, associations, and organizations such as Canadian Construction Women (CCW), Vancouver Regional Construction Association (VRCA), Canadian Association for Black Health and Safety Professionals, Safety Driven Technical Advisory Committee, and the BC Tradeswomen Society. It highlights her education and experience with women in the trades and construction, as well as being a visible minority.
Amandeep is passionate about tradeswomen’s rights, equal opportunities, diversity and inclusion, mentoring new and young workers, and mental health. This has led her to pursue a career path in health and safety.
In her spare time, Amandeep loves to kickbox, ride motorcycles, read, cook, go camping, quadding, 4x4ing, shooting, hiking, swimming, and enjoys going out to live sports events, games, concerts, and working out.
I would say general construction overall. Because I grew up around heavy equipment all my life, I always had such a passion of big pieces of machinery. I’m still in awe of heavy haulers and cranes. It’s fascinating to see what they can achieve. I took it upon myself to get my class 1 driver’s license and can run anything from 2 wheels to 18 wheelers as well as track equipment.
Shifting over into health and safety, I love the mental health aspect of our work. We all speak to visible hazards and injuries but there needs to be more focus on workers’ mental health and wellbeing. I’ve always had an interest in the psychological aspects of work.
The nice thing about it is no two days are the same in the day in the life of a health and safety consultant.
I can be meeting with clients to discuss safety management systems and strategies to out in the field on a job site doing project safety assessments to building/designing safety programs at home. There’s always 1 foot in the field and 1 foot in the office.
Contract work involves site support and client representation, assistance in pre-qualification and bid packs, site inspections, incident investigations, statistical tracking and trending analysis, subcontractor management, conducting gap analysis and much much more.
Another thing to note is, we wear various hats throughout the day, not only are we a one-stop-shop for safety, we can also act as counsellors and empathizers, a referee of sorts, a valuable resource or reference for other things.
There are many things that make a good safety consultant. They need to be flexible and versatile.
Safety consultants need to have the ability to shift from one space to the next and also have an overall understanding of a vast number of safety-related topics.
They need to be able to disseminate information for their clients in a timely manner. For this reason, strong communication skills are vital. There will be both written and verbal.
Safety consultants need to also multi-task and have strong problem-solving skills.
Most importantly, they need to be able to understand people, connect with them on many levels, and have empathy. I think that having the soft (people) skills is key to making a safety consultant good.
Safety is safety. But having said that, there are slight differences in North America.
I would say legislation and regulations are dictated by jurisdiction and to some extent by the governing bodies.
Though there is a lot of advocacy around workers’ safety and for workers’ rights, there continue to be some differences. The US has the Occupational Safety and Health Administration (OSHA) as the regulatory body whereas Canada has provincial regulatory agencies such as the Workers' Compensation Board (WCB).
There are definitely a lot of challenges around being a women in a heavily male-dominated industry. For a lack of better words, it’s still a man’s world in construction, oil and gas, and pipeline even in this day-in-age.
We still struggle to be heard and seen as equals despite efforts put in that meet or exceed our male-counterparts. We have to work twice as hard just to prove our worth.
To counter stereotypes, stigmas and challenges, there continue to be resources, support, and advocacy to educate our male-counterparts and empower fellow women. To say we are there would be a false depiction and understatement.
In terms of advantages, though we are grossly disadvantaged, we have strong communication skills. We have the ability to manage and resolve conflict using soft skills. We remain level-headed, professional, and conduct ourselves in such a manner to solve problems and issues. For this reason, we are also resilient.
I would say taking on a collaborative approach with all departments, and up and down the organizational chart. You need to have buy-in for a safety management system (SMS) to be used effectively and actually work.
Buy-in is needed from top management, leadership, supervision, right down to the end-user, the workers on the tools, boots on the ground. Without the spirit of consultation and collaboration, there is poor safety culture.
The most useful tool you have to implement safety measures is empowering your workforce and engagement from all levels.
Great question.
As we spearhead the dawn of new technologies and integration of digital systems, we continue to enhance SMSs with advantages and advancements.
A good example is that of digitizing SMS's. Instead of having paper copies of everything, forms, policies, procedures, programs, and systems can now easily be accessible at any time any place via devices.
This minimizes the workload making it more efficient and essentially giving more focus to in-person field presence.
https://ohsonline.com/home.aspx,https://www.ehstoday.com/
I would say LinkedIn and manufacturer websites. Also consulting with colleagues and being on different job sites, you see who’s implemented what and get some honest reviews.
Personally my iPhone and Fitbit smart watch. I also use an Amazon Echo Dot (Alexa) when I’m home. Professionally it would still be my phone and safety applications.
Yes absolutely. Get buy-in through having open forums or town halls. Encourage your work force to speak up, listen to them, and address issues / concerns.
Also follow up with workers. By having that open 2 way dialogue and engagement, you will foster a positive safety culture. To support this environment, there needs to be follow up and continued dialogue.
I would say change management with personnel needs to be navigated with a collaborative approach and clear concise communication.
By this I mean that having strong messaging often rules out misinterpretation. By having a clear vision of end goals, there is little room for uncertainty. There needs to be mutual patience and understanding from all parties.
I would say miscommunication is by far the biggest hazard on any project or site. Having solid systems and processes clearly communicated mitigates this.
Bottom line, everyone needs to be on the same page. SIMOPS (simultaneous operations) need to be conveyed to everyone on all work fronts.
Absolutely! We see this even now with the introduction/integration of technology and devices offering assistance where manpower was once needed.
An example of this is partially automated mining operations. The future is now and if we’re not on board, we will get left behind.
Artificial Intelligence is flawless in every essence of the phrase. It is immune to human error.
By saving time, money, efforts, we can refocus our attention to other areas needing attention.
We hope you enjoyed this article, you can read and learn from other industry experts from across the globe, and learn from their insights into health & safety in a variety of industries.
We think you'll also find the articles below really useful
Join 5,000 H&S professionals and sign up for the spacebands monthly newsletter and get the latest blogs, free resources, tools, widgets and a dose of health & safety humour.
spacebands is a multi-sensor wearable that monitors external, environmental hazards, anticipates potential accidents, and gives real-time data on stress in hazardous environments.